What you just heard was the sound of the future.
We are the leader of EV,
Why don't we specialize a sound that is really in line with the Nissan Intelligent Mobility strategy
and we found this sound that is a combination of harmony,
a combination of dynamism.
I'm sure that when you will walk on the street,
you hear the sound and without turning your head back, you will say that this is a Nissan.
We are moving forward on the Nissan Intelligent Mobility
in terms of timing, really spot on.
We have just launched also the New LEAF.
When you look at the IMx concept you can imagine what will come after,
so in terms of timing, it's really the right moment now to launch the sound.
Our vision is, as I say, with new LEAF that we just launched,
probably the New LEAF is the most (advanced) technological product on the street.
So our strategy is really the implementation of Intelligent Mobility.
We launched the New LEAF, the e-Power, the IMx concept
which really gives you our vision for the future of Intelligent Mobility.
We are talking about a future that is more mid-term than long-term.
When you look at the IMx, when you look at the LEAF Nismo,
when you look at our participation of Formula-E,
there is a very strong consistency of the implementation of Nissan Intelligent Mobility.
For more infomation >> Nissan's Daniele Schillaci at the 2017 Tokyo Motor Show - Duration: 1:54.-------------------------------------------
JUST GO-BEFORE 5: For How Long Do You Go Abroad - Duration: 4:40.
-------------------------------------------
Like father, like son: Man becomes Placer County deputy like his dad - Duration: 1:32.
-------------------------------------------
Once Upon a Time 7x04 Sneak Peek "Beauty" (SUB ITA) - Duration: 2:02.
-------------------------------------------
Mira la explosiva presentación de Pitbull en los Latin AMAs 2017 | LAMAS | Entretenimiento - Duration: 12:57.
-------------------------------------------
고영주 문재인 공산주의자 증거와 결론|KT-KR - Duration: 11:47.
-------------------------------------------
Prince Royce feliz de estar en los Latin AMAs | LAMAS | Entretenimiento - Duration: 1:27.
-------------------------------------------
Designated Survivor 2x06 Promo "Two Ships" (SUB ITA) - Duration: 0:30.
-------------------------------------------
Cоmo cambiar filtro de combustible MERCEDES-BENZ E W211 INSTRUCCIÓN | AUTODOC - Duration: 5:58.
Use a torx №T30
Use an end bit №5
-------------------------------------------
Basic course of cardboard furniture - Lesson 2 The structure of the table - Duration: 10:22.
Hello! We continue with the basic course
cardboard furniture. If you have not seen you Lesson 1
I recommend you see it before proceeding with this video. You have the link in the
Information box. Now, we begin with Lesson 2. To
realize the explanation I have decided that we will make a table
because it is something very simple but you can apply this information to
perform other furniture.
Let's see how to get measurements without being a furniture designer.
There are several ways to do this and this is how I do.
You must first measure the space where the furniture will go, taking measurements
tall, wide and long.
Being a table as high'm going to define me because in space
Real high at my disposal is the roof.
Then considering other furniture in the room,
I will set my table will have a height of between 55 and 60 centimeters.
For width as the table goes in the middle,
I have taken the measure considering that it can pass easily between
table and other furniture so it should be between 50 and 60 centimeters.
Continuing with this slogan, the length of the table should have no more than 70 centimeters.
Being aware of the space that we can now realize
measures table. For this we break down the main parts
They will form the cabinet. Will the board and legs. For
set the table height I have to take into account these two pieces. I go
choose 55 centimeters to the overall height and the measure I have to
distribute between the top height and leg height.
The logic is that the legs are much higher than the board.
So I decide that the legs will have a height of 50 centimeters and the
board five centimeters. The measurement of the board may be smaller or
greater depending on the thickness you want him. And with that we would have the high
table. The width of the table we will give board. Given the
measures of space, I'll decant by 50 centimeters.
For long we will also only consider
board and will choose the maximum space that were 70 centimeters.
We have the measures on the table now let's realize a few more pieces.
I even drawing a sketch awful
But it is necessary.
We had said that the board would have a width of 50 centimeters,
70 centimeters long and high, which is the thickness that will have the board,
It will be 5 centimeters. We are the legs. We can make them
with square base of this style, which is what we normally see on a table,
but I'll show a much easier way. Make with a round base
oval u. We had set up 50 centimeter so now
I have to take the diameter of the legs. How do we do it? What I do is
I do think that if a leg like this, the measure of each side would be 5
centimeters and do not know if it makes sense mathematically what
I say but this is what works for me. What I do is multiply the 5
number of sides having the legs, which are four, and the result gives me
I use to make the diameter of the oval leg.
We get down to work.
To make table legs, let's cut four pieces of cardboard 50
centimeters high. The length will depend on the thickness
carton but approximately be about 80 centimeters.
Let's grab a roll of cardboard or something similar and we used to crimp the piece.
We remove the roll and now we go rolling up the piece evenly and
gluing with hot glue.
As we enrrollándolo have to check the diameter measurement.
In this case we must reach 20 centimeters.
If the piece of cardboard is small we unite the other end and
we continue rolling. And if we have too, just cut. To soften the
bonding paste paper tape.
This is a quick and easy way to make
paws. We repeat this step three more times and
We subject these parts.
To make the board we need three pieces of 50 x 70 centimeters.
We grabbed one of them and we will make a margin of 2.5 centimeters.
You can make it smaller but I would not recommend.
Then just where the lines intersect margin
let's draw the outline of the legs. You can do it directly with the leg
or use an object of the same diameter so that it may be easier.
These circles have them cut and we will remain so. We booked this
piece and grabbed another board. Now let's fill this piece
cardboard strips. To know the size must take into account the height
we decided for the board. There were five centimeters. Let's gather
all parts of the board and measuring the height of all joints.
It measures one centimeter so this is what we subtract the total measure and we
will the measure should have high strips: four centimeters.
Cut strips four centimeters high and long in this case is the
board or less. And let's sticking with hot glue on one of the
board pieces. First the edges and then inside.
When we have completely filled be stuck another piece of board
above. To make it easier you can fold the cardboard in this way and
then paste sections with hot glue.
Thus when a part is already stuck you can go without hitting the rest
fear that the workpiece moves.
After be stuck over the part in which we marked the contour
paws. This can be done with white glue and
then put some weight on it or do it with hot glue.
Then make sure the joints with paper tape.
We have all the pieces ready
to join them.
To paste the legs what I do is put white glue in the center and
then hot silicone around WTD.
I put the leg and stuffing union with hot glue.
Repeat this step with the rest. We will being well and we can make cartapesta.
If you have any questions, lesson one in which I explain how.
Cartapesta brings quite hard to furniture but still
need to strengthen the part of the legs. Put a few pieces between the
legs. You can put them halfway up or just when the board ends. measures
distance between the outside of each of the legs.
In my case I need two pieces of 65 by 10 cm for the longest part
table and two pieces of 45 by 10 centimeters for the shorter part.
Check that you agree that these measures may vary due to the type of
cardboard and pressure exerted by winding legs. These pieces were
You have to make cartapesta on both sides and then glue them to the table.
This step could be done before the cartapesta but it seems to me more
comfortable doing separately.
And here comes Lesson 2.
In the next video we can see how to decorate
cardboard furniture and teach you how to give an appearance of aged wood to
table. Do not miss! And let me remind you
little hand up and says it is looking like the course.
Ciao!
-------------------------------------------
Funny Sphynx cat Casper walking on the background of yellow leaves in the new shoes composing haiku - Duration: 1:22.
-------------------------------------------
Paladins Strike Gameplay Mobile MOBA Action Game - Duration: 8:16.
-------------------------------------------
How to Make Gaming Steering Amazing Cardboard and Pipe - Mr Roy life hacks - Duration: 3:06.
How to Make Gaming Steering Amazing Cardboard and Pipe - Mr Roy life hacks
-------------------------------------------
Harajuku Kawaii Channel #12 Alice on Wednesday - Duration: 4:56.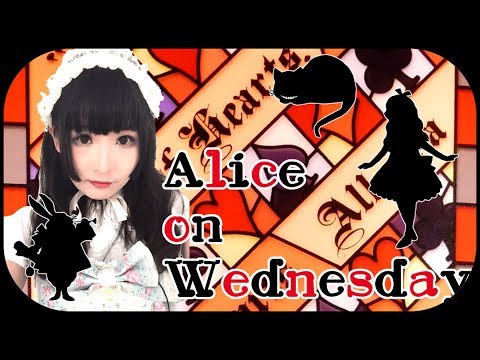
Find the shops with Alice motifs in Harajuku.
Hello, guys. This is Hamuka from Harajuku Kawaii Channel.
Today, I'm visiting this shop named "Alice on Wednesday"!
It's an accessory and sweet snack shop themed "Alice in Wonderland".
Look at this.
The exterior looks like the world-view of "Alice in Wonderland".
OK, let's go.
"Alice in Wednesday" is an accessory and sweet snack shop
themed from Lewis Carroll's novel "Alice in Wonderland".
The shop name "Wednesday" means "Let the most boring Wednesday in a week special".
The store has 3 floors and there are about 3000 kinds of items displayed.
Please watch your head because entrance is low.
This is the 3rd floor, "Atelier of Hatter".
The theme of this room is an atelier of the Hatter who attend a mad tea party in the Alice's story.
In this room, products, mainly fashion accessories such as bags and pouches are placed.
Also in the back is a stained glass designed to be a hat.
These tote bags have the original illustration on them.
It is irresistible for Alice fans!
There are lots of tricks on the stairs.
There are pictures of Alice on the wall from the second floor to the third floor.
They express the Alice's world-view.
The impressive character is the Cheshire Cat.
You can have eye contact with him from anywhere.
This is the 2nd floor, "Court of the Red Queen".
This room is themed from Queen of Hearts' trial.
There are many interiors themed from it.
You can sit in the Queen's chair and take photos.
I would like to take a picture in the absence of the queen.
In this room, there are accessories.
They are very kawaii.
They express Alice's world-view such as Alice's silhouette, rabbits, and rose flowers.
And they relives my girlhood.
I'm glad that all the prices are reasonable, from around 600 yen.
The staircase leading from the first floor to the second floor is named "Mushrooms forest".
Mysterious mushrooms are lined up.
On the top of the mushroom, a caterpillar is sucking a water pipe.
It's like the one from the picture book.
In contrast to the solemn atmosphere, there is a white room looks like kitchen in the ground floor.
This room is named "White Queen's kitchen".
Here you can get snacks which express Alice's world-view.
The interior that imitated the kitchen is decorated also in the ceiling.
This "Drink me cider" stands out here.
It's themed from the one Alice drinks in the original story.
How does it taste?
This "Eat me cookie" is also themed from the one Alice drinks in the original story.
This one is handmade.
Every item is kawaii so I can't decide!
This is a chocolate box looks like a hat.
You can buy one as a souvenir because the package is impactful.
Today I visited an accessory and sweet snack shop, "Alice on Wednesday".
There are many mysterious tricks,
so I enjoyed it as if I were Alice.
Don't forget to visit here when you come to Harajuku.
Bye~~~
-------------------------------------------
Bangla News 27 Octobor 2017 Bangladesh latest news Today bangla Breaking News BD News all bangla. - Duration: 12:05.
Bangla News 27 Octobor 2017 Bangladesh latest news Today bangla Breaking News BD News all bangla.
-------------------------------------------
Bad Bunny habla de su outfit en los Latin AMAs | LAMAS | Entretenimiento - Duration: 1:21.
-------------------------------------------
[Interview] Matsuzaki Yoshiaki - Japanese Bokken Artisan (Part 1/2) - Duration: 17:26.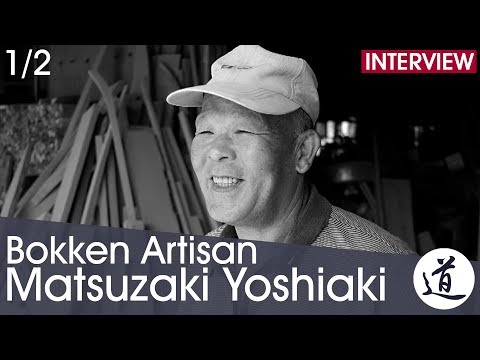
Enjoying the quiet summer months,
we travelled across Japan to Miyakonojo and the Kirishima sankei region
to visit one of the last wooden weapon workshops of Japan:
"Matsuzaki Bokuto Seisakujo".
The founder, Master Matsuzaki Yoshinori switched from agricultural tools to
the manufacture of Bokken 1969.
The tradition is perpetuated today by the founder's son, Master Matsuzaki Yoshiaki,
assisted by his son, Matsuzaki Yoshimasa.
My workshop's date of foundation?
Let me see.. maybe...
Well, the official one is something like Showa 40-something.
Showa 44 (1969), 43 (1968) or 44 (1969) I think.
I can't remember it exactly.
But it must've been around 44 (1969).
But before that, we were making wooden tools.
Then we officially changed to Bokken manufacturing,
starting in Showa 44 (1969).
I think that's approximately when we started manufacturing Bokken.
Then...
My father continued manufacturing Bokken,
and I started at my father's workshop when I was 18,
and learned the craft.
At the time, there were 4 craftsmen,
5 including my father and 2 (factory) workers.
Further 4-5 helper, doing the sanding and varnishing.
So when I came back from school and started at the workshop,
we were thinking about stabilizing on 14 or 15 people...
And back then, everything was completely hand made.
We didn't have machines like those we have today,
and a craftsman could within a day make about 35 pieces, planing only.
40 pieces at most... but we'd still have to sand and varnish or polish them.
So, in those days...
When we started to sell Bokken
no matter how much we made, it was never enough.
We've customers with whom we've been
doing business for about 50 years.
From since my father started.
So two of these clients we had for about 50 years,
and others for 30 years, or something
over 20 years.
The reason why we could without
worries manufacture Bokken
was because we had these relations.
From the time we started, they would purchase
almost 100% of the products from us.
So, as I told you before, we didn't have to compete
with an excessively low price.
So that's why we could do it
and actually still can.
As far as I know
there were 15 or 16 companies I think.
Some of them would work as individuals.
Artisans who were formerly agricultural tools craftsmen
switched over to produce Bokken.
So some artisans were making Bokken on a freelance basis.
In those places, there was no successor,
so they would naturally retire and their company disappear.
You can't say it exactly like that, but in a certain way, they didn't have the people and their business failed.
In the end, the cause was the cheap selling
that lead to an increase in debts.
So certain businesses went
bankrupt like that.
That's why there were several cases where the business couldn't be continued
because there was no successor
or because they were pushed into bankruptcy.
Well, some disappeared for those reasons, and now...
there are only 4 workshops remaining.
Because we had successors.
Like me and the sons of the other workshops,
we were taught the art and took over.
That's why today, there are 4 workshops left.
Well, those left are those with successors.
The tip of the Bokken is slightly
thinner than that of the others.
Like those we're making at the workshop...
That's my father who first made that kind of Bokken.
Well..
I don't know his name, but one of these
long time business partners came to see my father...
that was 50 years ago and at that time
there was still room to improve our Bokken...
Those clients who were selling martial arts articles,
who've passed away now, asked my father
to make the Bokken in a specific shape. They discussed it and
in the end, the shape was decided like that.
So my father created this product based on
the discussions with the main clients,
and this shape got popular (was spread) among them
and hence, I (my generation) can't decide to
change the shape of our Bokken all of a sudden.
But also, I like the style of my father's Bokken.
I think it's the best.
That's why also in the present,
I still make the Bokken in the shape my father developed,
and I tell my son that
I'd like him to keep this shape as well.
This is the special characteristic of our model.
At a first glance, you might not see the difference,
but we as artisans, we can tell which workshop has made it,
master Horinouchi, master Nidome or master Aramaki.
We see it immediately.
And my father always used to say
"don't start cutting corner, even if it's just the finish, just because you're busy!"
At least a minimum of sanding
and then the varnish - back then. In our days now
it's quite popular to spray them, but we still
varnish them with pads, rubbing it.
Because, varnishing is actually quite satisfying.
Using pads might not seem very effective, but...
A teacher of a furniture dealer,
he told us when we all were assembled,
"The basic of wood coating is varnishing with pads"
So that's what he taught us.
We bought a compressor,
and gave it a try.
The varnish was used up in a blink.
You throw away half of it. With pads, you use 100%.
There's no waste. And that's what I was taught as basic.
And I still think that it's the best way to do it.
This is how we do it, using this technique.
But I don't judge which is better - you also get a
nice result using spray. But we, we do it our way.
The Japanese word "shokunin" (職人) is defined in Japanese and Japanese-English dictionaries
as 'craftsman' or 'artisan,'
but such a literal description does not fully express the deeper meaning.
The Japanese apprentice is taught that shokunin means not only having technical skills,
but also implies an attitude and social consciousness.
The shokunin has a social obligation to work his/her best for the general welfare of the people.
This obligation is both spiritual and material,
in that no matter what it is, the shokunin's responsibility is to fulfill the requirement.
ーToshio Odate, Artist and Teacher
The part that is really hard?
hmm..
..there's no such "hardship" concerning work,
but lately, because of my age,
my eyes are not as good as they used to be.
So when I look at a Booken like this,
I can see my hands clearly, but the tip is blurry.
Even if I wear glasses, I still can't see the whole piece clearly.
Indeed, my physical strength is decreasing.
As for example my eyesight.
These are the things that happen
I cannot do the measuring of custom made products
easily by myself, like I used to.
My son checks the dimensions,
the execution of the Mine, of the Shinogi etc.
These are the things he checks for me.
Recently, those difficult handmade tasks -
it's not that I can't do them anymore,
but compared to the olden days, I Iost confidence, little by little.
But particular hardships.. Of course, there are
the difficulties of stocking material etc. but I don't
really consider these as hardships.
It's rather the "course of events", it's how it is nowadays.
But, growing old(er), little by little,
I can't do the various custom made orders
exactly as I want to anymore.
I can feel that.
And that's been becoming annoying, lately.
The custom made orders.
Making those custom made orders. That became troublesome.
But thinking about it like that, I naturally hand over to my son.
That's the natural flow of things, right?
So it's my son who does it, and he can do it by himself.
What I like?
Well, it's not that I don't like work of course
But I'd rather just live enjoying myself.
But having a simple piece of timber,
a raw material, that I could change into a product.
Well.. It's (to start) from a simple tree. Making a nice product,
one better than I had imagined myself.
To the finish of the wood color.
Those are very pleasant moments,
that's when I'm satisfied, and happy.
When the result turns out to be better than I thought.
When I look at it after finishing and think:
"ah, I did a good object".
Depending on the quality of the timber...
That timber becomes like this maybe..
This non-discript timber...
when polishing it like this or doing that and finishing it,
the grain becomes unbelievably stunning. That the surface of the wood becomes nice,
you can already guess it, when you see the timber.
I like wood...
I really like the wood.
I use oil for Sunuke and ebony,
to reveal their particularities.
If Sunuke, or Kokutan...
isn't oiled, it'll cleave and get cracks.
Even if you keep the finished product in a room.
If you have a heater or air conditioner, it will crack.
That's mainly the reason why these timbers are oiled.
Using varnish for the oak.
We have some over there,
the oak I'm using.
We put it into a steaming oven...
when the timber starts to swell up
we put it in the steaming oven and take off the oil and scum.
But if we'd keep it like this, its appearance and color wouldn't look nice.
Originally, and even if called 'red' oak, if it dries naturally
it becomes whitish or yellowish.
But if you steam it, oil it, and let it dry for a year,
if you varnish it after that, the color becomes red.
That's why we varnish it.
It's specific to the type of wood.
To get the best out of it,
we'd either varnish or leave it like that.
But we can actually use the timber to our liking.
So if it was just me, I'd leave the white oak unvarnished as much as possible.
But with white oak it's difficult.
Sometimes, there is some that is completely white.
But during the drying process, the color almost looks burnt,
when the water doesn't evaporate completely and some is left, it becomes darker,
There's not just outstanding and totally white timber.
That's how it is.
With our hands, we now have to use the timber in the best way we can, racking our brains.
We're actually thankful for that.
Sending out products, sending out objects, selling them,
we're thankful for that.
However,
I say that to our regular customers, and to Seido as well,
It is quite hard to respect the appointed day of delivery, having ready all items.
At our workshop, it's only me and my son.
The orders of our most important clients pile up during the same period, and for the same products.
And everyone wants to get the items quickly.
Till that and that date the orders have to be sent out.
From January...
Actually from the end of November, we start getting busy.
So from November, over New Years, January till May, until the national holidays in May,
we work with barely a day off.
That's how busy we are.
But in this industry, it has always been like this.
During summer, until now, there were calm periods when we hadn't to send out any products.
We did our best during busy times.
And during summer, we could slow down a bit.
But the last few years... the no such summer break anymore.
Now, we receive orders continuously
and we're always pressed to meet the deadlines.
But this said, having work, receiving orders,
for us and for our work, we're thankful and happy about it.
Although it's physically tough, we do our best every day.
That's how it is.
Không có nhận xét nào:
Đăng nhận xét